Item Cost included in Standard Cost of Production BoM but not respective Production Order
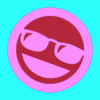
andrew_tingey
Member Posts: 2
Afternoon all,
We're currently working Navision Classic 2009, Manufacturing environment.
Struggling at the moment to keep on top of items that are more suited to being on KANBAN as opposed to automatically adjusted inventory stock. We need to have these items on the Production BoMs such that the respective costs are pulled together into the complete machine cost (for quoting purposes etc.) however don't then want the respective Production Order generated from this Production BoM to incorporate the costs for these items. Essentially we don't want to book these items against the Production Orders as the quantities aren't necessarily accurate, and are mostly very low value but relatively high usage parts (fixings etc.).
What I want to do is enable these items to have the inventory manually adjusted every time the box is emptied (i.e. the inventory would be 100 when there's a box on the shelf, 0 when no box and nothing in between). This cost would be booked to a consumable cost centre which we already have set up.
Currently these items are on backwards flushing, so whenever a Pick is created the system automatically consumes the number of fixings on the BoM to said build and reduces the inventory by that amount. Problem is that these items are line side so fitters just grab a handful whenever they need them, meaning the inventory is immediately incorrect on Nav and as such we have no end of stocking issues (either way to many or way too little). Essentially we want to make this a manual process, but still enable the costs of these items to be pulled through onto the standard cost of the Production BoM but not then considered on the Production Order, otherwise we'll end up either a cost variance (if the items are ignored on the Pick for example) or the inventory is always going to be incorrect.
Does this make any sense and, if so, is there a function on the item card that can be selected which will allow the above?
We're currently working Navision Classic 2009, Manufacturing environment.
Struggling at the moment to keep on top of items that are more suited to being on KANBAN as opposed to automatically adjusted inventory stock. We need to have these items on the Production BoMs such that the respective costs are pulled together into the complete machine cost (for quoting purposes etc.) however don't then want the respective Production Order generated from this Production BoM to incorporate the costs for these items. Essentially we don't want to book these items against the Production Orders as the quantities aren't necessarily accurate, and are mostly very low value but relatively high usage parts (fixings etc.).
What I want to do is enable these items to have the inventory manually adjusted every time the box is emptied (i.e. the inventory would be 100 when there's a box on the shelf, 0 when no box and nothing in between). This cost would be booked to a consumable cost centre which we already have set up.
Currently these items are on backwards flushing, so whenever a Pick is created the system automatically consumes the number of fixings on the BoM to said build and reduces the inventory by that amount. Problem is that these items are line side so fitters just grab a handful whenever they need them, meaning the inventory is immediately incorrect on Nav and as such we have no end of stocking issues (either way to many or way too little). Essentially we want to make this a manual process, but still enable the costs of these items to be pulled through onto the standard cost of the Production BoM but not then considered on the Production Order, otherwise we'll end up either a cost variance (if the items are ignored on the Pick for example) or the inventory is always going to be incorrect.
Does this make any sense and, if so, is there a function on the item card that can be selected which will allow the above?
0
Answers
-
The best way to resolve this is to make use of Kanban cards. Kanban cards are used to regulate and control the flow of parts from suppliers and into production. They are used to ensure the right parts are available when needed, without the need for manual stock adjustments. Each card specifies the amount of parts to be ordered, and can be easily adjusted to accommodate changing demand. By using Kanban cards, your stock will always be up to date and you won't need to manually adjust the inventory. Additionally, Kanban cards can be used to track costs associated with the parts, allowing you to accurately determine the cost of the production BoM.0
-
Good morning, thanks for this. I've never heard of a Kanban card, where would these be located within Navision? Also, how would Navision know when there isn't any stock left without a manual adjustment of the inventory - without the manual adjustment we'd be running off of Production BoM data which I can't guarantee will be accurate against the "handful" of bits our Production team may take from the bin at one time.
We currently account for this difference as a "loss" against a consumable cost centre, what I need to avoid is that variance being applied to a machine Production Order as this would then show the machine sale has generated less income than it should, whereas the consumable cost centre is a budgeted overhead.0
Categories
- All Categories
- 73 General
- 73 Announcements
- 66.6K Microsoft Dynamics NAV
- 18.7K NAV Three Tier
- 38.4K NAV/Navision Classic Client
- 3.6K Navision Attain
- 2.4K Navision Financials
- 116 Navision DOS
- 851 Navision e-Commerce
- 1K NAV Tips & Tricks
- 772 NAV Dutch speaking only
- 617 NAV Courses, Exams & Certification
- 2K Microsoft Dynamics-Other
- 1.5K Dynamics AX
- 320 Dynamics CRM
- 111 Dynamics GP
- 10 Dynamics SL
- 1.5K Other
- 990 SQL General
- 383 SQL Performance
- 34 SQL Tips & Tricks
- 35 Design Patterns (General & Best Practices)
- 1 Architectural Patterns
- 10 Design Patterns
- 5 Implementation Patterns
- 53 3rd Party Products, Services & Events
- 1.6K General
- 1.1K General Chat
- 1.6K Website
- 83 Testing
- 1.2K Download section
- 23 How Tos section
- 252 Feedback
- 12 NAV TechDays 2013 Sessions
- 13 NAV TechDays 2012 Sessions