Alternative Replenishments & Planning Improvements Tool
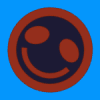
krola
Member Posts: 2
Hi All,
I am looking for a solution - external app or company who had already developed solution which could cover below scenarios.
Any suggestions will be highly appreciated.
Thank you!
Scenario 1.
Item is set as to be purchased (Replenishment Method = Purchase). Lead Time connected with purchasing: 8D.
Item can be also produced. Lead Time connected with production: 3D.
We receive an order for this Item today which should be shipped in 6D.
Let’s assume we have no stock.
We will not receive Items from Vendor on Time as it takes 8D to purchase it according to default Replenishment Method (which should stay like that).
We need a tool which could analyze Item Availability and alternative Replenishments (including alternative lead times of those).
Scenario 2.
Item is set as to be produced. Lead Time connected with production: 5D.
Let’s assume we have no stock.
The bottleneck Work Center which is used in production process of this Item is fully booked for 20 days ahead, therefore producing this Item can be started in 21 days, therefore can be finished in 25 days.
We need a tool which could analyze Freeze Time (time fully booked) and real Item Lead Time to specify what is the first possible day when Item can be available. It should also analyze Item Availability in Time as it may happen that already created supply will cover demand.
Capacity Constrained Resources cannot be used as we cannot rely on routings – only Lead Times.
Moreover, for Assembled Items we need be able to set such Freeze Time or the tool should analyze BOM Tree recursive.
Scenario 3.
Item is being produced in house, it has routing assigned. But in case when size of production will be higher than X we would like to use another routing – different work centers, including subcontractors.
We need a tool which could overwrite routing from Item Card automatically, whenever Production Order is created (from Sales Order, Planning Worksheet or manually) if some conditions will be met.
Scenario 4.
Item is being produced. We consume sheets of steel. In BOM there is one, specific size of steel sheet. But it is possible to produce the same Item from the same steel, which will come from a sheets with different size which is represented by another Item No.
With standard functionality, Requisition Worksheet will get crazy.
Alternative option – use Item Substitutes but that process should be automated and the tool should cover such automation.
Scenario 5.
There is finished good item which is produced in house. Let’s say that normally we produce it from steel 0.6 mm, but we run of stock of this components and we have to wait long for new purchase receipt. Therefore we decide to start producing from 0.8mm steel. This will cost us more, but we will be able to deliver goods on time. Moreover, once we produce from 0.6 mm we cut it on manual cutting work center. Once we produce it from 0.8mm we cut in on laser work center.
We were thinking about two adjustments: linking Production BOMs with Routing and making them relying on each other and functionality which could automatically replace BOM and/or Routing when problem with availability of components will be noticed.
Scenario 6.
In Production order components we have an Item which have Replenishment Method = Purchase and 30D lead time. We keep safety stock on it.
It may happen that we will run out of the Item therefore we need to decide that we will produce the Item in house – 15D lead time. System should support us in update of suggestion which is coming from Replenishment Method in Item Card/SKU.
Scenario 7.
We are managing consignment stocks. Once a week we receive information from our Customer what was used – we are doing then shipment and issuing the invoice and also creating replenishment. For such demands we have Maximum Inventory or Lot for Lot (with safety stock) as Reordering Policy. When Planning Worksheet will suggest replenishment, Due Date will be set for today, so the order will be created as urgent. But Production Department will not be able to produce it today, as we have Production blocked for next 20D (Freeze Time mentioned in point 2.). That means we need to create supply which will be started in 20D (after freeze time) and disables Planning Flexibility on Production Order.
I am looking for a solution - external app or company who had already developed solution which could cover below scenarios.
Any suggestions will be highly appreciated.
Thank you!
Scenario 1.
Item is set as to be purchased (Replenishment Method = Purchase). Lead Time connected with purchasing: 8D.
Item can be also produced. Lead Time connected with production: 3D.
We receive an order for this Item today which should be shipped in 6D.
Let’s assume we have no stock.
We will not receive Items from Vendor on Time as it takes 8D to purchase it according to default Replenishment Method (which should stay like that).
We need a tool which could analyze Item Availability and alternative Replenishments (including alternative lead times of those).
Scenario 2.
Item is set as to be produced. Lead Time connected with production: 5D.
Let’s assume we have no stock.
The bottleneck Work Center which is used in production process of this Item is fully booked for 20 days ahead, therefore producing this Item can be started in 21 days, therefore can be finished in 25 days.
We need a tool which could analyze Freeze Time (time fully booked) and real Item Lead Time to specify what is the first possible day when Item can be available. It should also analyze Item Availability in Time as it may happen that already created supply will cover demand.
Capacity Constrained Resources cannot be used as we cannot rely on routings – only Lead Times.
Moreover, for Assembled Items we need be able to set such Freeze Time or the tool should analyze BOM Tree recursive.
Scenario 3.
Item is being produced in house, it has routing assigned. But in case when size of production will be higher than X we would like to use another routing – different work centers, including subcontractors.
We need a tool which could overwrite routing from Item Card automatically, whenever Production Order is created (from Sales Order, Planning Worksheet or manually) if some conditions will be met.
Scenario 4.
Item is being produced. We consume sheets of steel. In BOM there is one, specific size of steel sheet. But it is possible to produce the same Item from the same steel, which will come from a sheets with different size which is represented by another Item No.
With standard functionality, Requisition Worksheet will get crazy.
Alternative option – use Item Substitutes but that process should be automated and the tool should cover such automation.
Scenario 5.
There is finished good item which is produced in house. Let’s say that normally we produce it from steel 0.6 mm, but we run of stock of this components and we have to wait long for new purchase receipt. Therefore we decide to start producing from 0.8mm steel. This will cost us more, but we will be able to deliver goods on time. Moreover, once we produce from 0.6 mm we cut it on manual cutting work center. Once we produce it from 0.8mm we cut in on laser work center.
We were thinking about two adjustments: linking Production BOMs with Routing and making them relying on each other and functionality which could automatically replace BOM and/or Routing when problem with availability of components will be noticed.
Scenario 6.
In Production order components we have an Item which have Replenishment Method = Purchase and 30D lead time. We keep safety stock on it.
It may happen that we will run out of the Item therefore we need to decide that we will produce the Item in house – 15D lead time. System should support us in update of suggestion which is coming from Replenishment Method in Item Card/SKU.
Scenario 7.
We are managing consignment stocks. Once a week we receive information from our Customer what was used – we are doing then shipment and issuing the invoice and also creating replenishment. For such demands we have Maximum Inventory or Lot for Lot (with safety stock) as Reordering Policy. When Planning Worksheet will suggest replenishment, Due Date will be set for today, so the order will be created as urgent. But Production Department will not be able to produce it today, as we have Production blocked for next 20D (Freeze Time mentioned in point 2.). That means we need to create supply which will be started in 20D (after freeze time) and disables Planning Flexibility on Production Order.
0
Answers
-
This is not the place for this as this is just for developers. Go ask a consultancy company and they will quote for you.
0 -
While I wouldn't say this site is strictly developers, you might try posting your question to https://www.dynamicsuser.net/. That site tends to have a much larger consultant audience.
There are no bugs - only undocumented features.1
Categories
- All Categories
- 73 General
- 73 Announcements
- 66.6K Microsoft Dynamics NAV
- 18.7K NAV Three Tier
- 38.4K NAV/Navision Classic Client
- 3.6K Navision Attain
- 2.4K Navision Financials
- 116 Navision DOS
- 851 Navision e-Commerce
- 1K NAV Tips & Tricks
- 772 NAV Dutch speaking only
- 617 NAV Courses, Exams & Certification
- 2K Microsoft Dynamics-Other
- 1.5K Dynamics AX
- 320 Dynamics CRM
- 111 Dynamics GP
- 10 Dynamics SL
- 1.5K Other
- 990 SQL General
- 383 SQL Performance
- 34 SQL Tips & Tricks
- 35 Design Patterns (General & Best Practices)
- 1 Architectural Patterns
- 10 Design Patterns
- 5 Implementation Patterns
- 53 3rd Party Products, Services & Events
- 1.6K General
- 1.1K General Chat
- 1.6K Website
- 83 Testing
- 1.2K Download section
- 23 How Tos section
- 252 Feedback
- 12 NAV TechDays 2013 Sessions
- 13 NAV TechDays 2012 Sessions