Basic Manufacturing Question
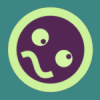
spena
Member Posts: 45
Hi,
I'm trying to determine the necessary steps to post production output in the production journal. I've read in several articles that "only the output quantity on the last journal line with the entry type Output will adjust inventory level when posting the journal."
So if I have a production order for 10 units, and actually produce one unit each month, what is the best, most efficient way to do so? Specifically:
- Do I have to enter an Output Quantity on each operation, that is NOT the last operation, for each of the 10 postings?
- Do I need to mark Finished on each operation, for each of the 10 postings?
- Do I need to enter Setup and Run time on each output posting for each of the 10 postings?
Any guidance would be much appreciated.
Thanks,
Steve
I'm trying to determine the necessary steps to post production output in the production journal. I've read in several articles that "only the output quantity on the last journal line with the entry type Output will adjust inventory level when posting the journal."
So if I have a production order for 10 units, and actually produce one unit each month, what is the best, most efficient way to do so? Specifically:
- Do I have to enter an Output Quantity on each operation, that is NOT the last operation, for each of the 10 postings?
- Do I need to mark Finished on each operation, for each of the 10 postings?
- Do I need to enter Setup and Run time on each output posting for each of the 10 postings?
Any guidance would be much appreciated.
Thanks,
Steve
0
Answers
-
Yes, if you want to consider its costs.
No, you don´t need to mark Finished
Yes, if you want to consider its cost
Each routing (operation) is defined to either show progress or to add cost, eventually it is the last routing that results in the item ledger entry, meaning adding the output into inventory. Lets say you have two routings; painting and final assembly. No matter how much you post output on the painting routing it will not result in a finished item, only the output you post on final assembly.
0 -
Hi,
Thank you for your reply. Have you heard of anyone customizing the production or output journal? My concern is we may have routings with over 20 operations, and manually entering or overriding the output quantity seems very inefficient.
In our environment, we must manually flush material, and setting the preset output quantity to Expected Output or Zero will still require the user to manually enter the output. If we need to enter 20 output journals for a long-lasting order, this can be very time consuming (20 operations x 20 individual output journals = 400 manually-entered lines).
Any input/ideas would be much appreciated. I was thinking to create a custom "Output Quantity" on the production journal, that would roll down to all operations.
0 -
Using expected output and production journal you will have expected output on all operations and if the quantity is as expected then just post the journal. But if you mean you normally have partial output (or different from expected) I would go for the customization to roll down the quantity on all operations.0
Categories
- All Categories
- 73 General
- 73 Announcements
- 66.6K Microsoft Dynamics NAV
- 18.7K NAV Three Tier
- 38.4K NAV/Navision Classic Client
- 3.6K Navision Attain
- 2.4K Navision Financials
- 116 Navision DOS
- 851 Navision e-Commerce
- 1K NAV Tips & Tricks
- 772 NAV Dutch speaking only
- 617 NAV Courses, Exams & Certification
- 2K Microsoft Dynamics-Other
- 1.5K Dynamics AX
- 320 Dynamics CRM
- 111 Dynamics GP
- 10 Dynamics SL
- 1.5K Other
- 990 SQL General
- 383 SQL Performance
- 34 SQL Tips & Tricks
- 35 Design Patterns (General & Best Practices)
- 1 Architectural Patterns
- 10 Design Patterns
- 5 Implementation Patterns
- 53 3rd Party Products, Services & Events
- 1.6K General
- 1.1K General Chat
- 1.6K Website
- 83 Testing
- 1.2K Download section
- 23 How Tos section
- 252 Feedback
- 12 NAV TechDays 2013 Sessions
- 13 NAV TechDays 2012 Sessions