Excluding held inventory from planning availability
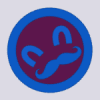
Fisherman
Member Posts: 456
I think I know the answer to this question, but I'm going to ask it in the interest of being thorough.
We have a business process where we move materials to a QC area/bin/zone for inspection in cases of damages or other quality issues. Where that happens, my operations team would like the ability to exclude that material from availability for planning/MRP. Is there any way to make that happen? We had considered using transfer orders to move the material to a location code instead of a bin, but wanted to verify first.
I have a feeling the answer is going to be "no", "not without modifications" or "You really don't want to do that..." since movements to a bin occur in Warehouse Entry and not ILE, but just thought I'd check...
We have a business process where we move materials to a QC area/bin/zone for inspection in cases of damages or other quality issues. Where that happens, my operations team would like the ability to exclude that material from availability for planning/MRP. Is there any way to make that happen? We had considered using transfer orders to move the material to a location code instead of a bin, but wanted to verify first.
I have a feeling the answer is going to be "no", "not without modifications" or "You really don't want to do that..." since movements to a bin occur in Warehouse Entry and not ILE, but just thought I'd check...
0
Comments
-
Hi
Yes, you need to make transfer order to exclude it from planning availability. and define Location filter while running Calculate regenerative planUday Mer | MS Dynamics NAV Techno-Functional Consultant0 -
And to confirm your fears, yes, you need a modification to exclude specific bins. We've done this before, and it's a little bit complicated (given the lack of a direct link between bins and the item ledger entries used for supply in MRP).
And instead of transfer orders, you can use the reclass journal (or whse reclass if using directed pick) to move the items to a new location. Saves a bit of time/complexity as compared to transfer orders (especially if using directed pick or any of the warehouse documents).0 -
What did you end up doing to resolve this?0
-
After reading through MRP availability calculations and testing, we decided to put materials that were subject to vendor return on a Purchase Return Order. It reduces availability by the quantity on the PRO.
As soon as we determine that we cannot ship the materials back to the vendor, we adjust those quantities out.
We could not use transfer orders to move materials out to another location, because our inventory costs are managed by location, and doing this created issues in tracking inventory valuation for any given location. Our Accounting said no.
The other options we looked at were modifying logic in MRP to look to bins with a certain bin type code, having planners add those quantities to safety stock, or even creating a hold ledger of some sort where people could record holds and using a SIFT index to reduce availability for them.
None of them were terribly good options. The first because anyone with a scanner could potentially move materials into a bin, which means that they could unintentionally affect planning, the second because it becomes too difficult to manage, and the third because we're not terribly comfortable building an entirely new process that impacts availability.0
Categories
- All Categories
- 73 General
- 73 Announcements
- 66.6K Microsoft Dynamics NAV
- 18.7K NAV Three Tier
- 38.4K NAV/Navision Classic Client
- 3.6K Navision Attain
- 2.4K Navision Financials
- 116 Navision DOS
- 851 Navision e-Commerce
- 1K NAV Tips & Tricks
- 772 NAV Dutch speaking only
- 617 NAV Courses, Exams & Certification
- 2K Microsoft Dynamics-Other
- 1.5K Dynamics AX
- 320 Dynamics CRM
- 111 Dynamics GP
- 10 Dynamics SL
- 1.5K Other
- 990 SQL General
- 383 SQL Performance
- 34 SQL Tips & Tricks
- 35 Design Patterns (General & Best Practices)
- 1 Architectural Patterns
- 10 Design Patterns
- 5 Implementation Patterns
- 53 3rd Party Products, Services & Events
- 1.6K General
- 1.1K General Chat
- 1.6K Website
- 83 Testing
- 1.2K Download section
- 23 How Tos section
- 252 Feedback
- 12 NAV TechDays 2013 Sessions
- 13 NAV TechDays 2012 Sessions