What's better: Enter a new item no. or use the variant code?
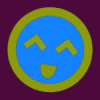
Rallnus
Member Posts: 79
Hello,
we are discussing about the question above.
Which advantages / disadvantages did you experience for the different solutions?
Thanks, Ralph
we are discussing about the question above.
Which advantages / disadvantages did you experience for the different solutions?
Thanks, Ralph
Rallnus (Yamaha FJ1200 - '89 / 25th anniversary was great!)
0
Answers
-
It depends on your business need. What is your requirement exactly ?0
-
my main question is if the variant code can fulfill the same functions as a item can do.
I think when you start with variant code you have to:
- change your settings
- create stockkeeping units for all variants
- find a solution to handle different pictures
- make all variant fields visible in the different forms
- set some more filters if you have created some reports for figures as like inventory, sales and so on
- change a lot of keys to get a better performance
- ...
What are the advantages of the variant code?Rallnus (Yamaha FJ1200 - '89 / 25th anniversary was great!)0 -
Rallnus wrote:my main question is if the variant code can fulfill the same functions as a item can do.
I think when you start with variant code you have to:
- change your settings
- create stockkeeping units for all variants
- find a solution to handle different pictures
- make all variant fields visible in the different forms
- set some more filters if you have created some reports for figures as like inventory, sales and so on
- change a lot of keys to get a better performance
- ...
What are the advantages of the variant code?
I agree with chengalasettyvsrao, the issue here is defining the business need. Don't look at what code you need to solve the issue until you know what the issue is. What are the reasons for this particular customer to use variants and what are the reasons not to use variants. Define that and then you can start asking questions.David Singleton0 -
In general, Variants are used for variations of the same Item. The classic example is always the clothing industry. Say you have this Star Wars T-shirt with a picture of the Death Star. Say you have this T-shirt in 4 different colors, and each color comes in 3 different sizes. Some people will argue that they are all the same shirt, other people will argue that different colors mean different shirts. For NAV it makes no difference, it's just data stored in tables.
You can make a case to have just one Item, and have a Variant for each Size/Color combination (1 item with 12 Stockkeeping Units). You can also make a case to have a separate Item for each color and have Variants for sizes (4 items with 3 Stockkeeping Units each).
Which one is chosen is up to the business. There's no 'right answer' or 'wrong answer'. Put it in test, play around with it. Find a good middle ground that makes sense to the business.0 -
DenSter wrote:Which one is chosen is up to the business. There's no 'right answer' or 'wrong answer'. Put it in test, play around with it. Find a good middle ground that makes sense to the business.
:thumbsup: :thumbsup: :thumbsup:David Singleton0 -
Most of the standard NAV reports and information forms (Item by Location etc.) shows information at Item level only and not on item variant level and before opting Item Variant consider this.CA Sandeep Singla
http://ssdynamics.co.in0 -
Standard NAV Stock Keeping units does not have the Production BOM , Routing functionality.0
-
ssingla wrote:Most of the standard NAV reports and information forms (Item by Location etc.) shows information at Item level only and not on item variant level and before opting Item Variant consider this.
I think we can use the Variant filter option in most of the reports to know the variant wise Qtyhansika0 -
chengalasettyvsrao wrote:Standard NAV Stock Keeping units does not have the Production BOM , Routing functionality.
Means that if you need a different BOM for a different Variant, the system needs you to create a new Item.0 -
DenSter wrote:
Means that if you need a different BOM for a different Variant, the system needs you to create a new Item.
He has to consider this point also if they go for variant functionality.0 -
I'll give you an example.
We are producing an item 4711 at various subsidarie.
For our customers it is the same item, the place of production doesn't matter for the customer.
The routing ist different because we've got different work groups.
If I follow your proposal I should install different items - or not?
Wouldn't I be the right way to build a relationship between stockkeeping units and routings?
(maybe BOM too...)
When we start a production order I will be depending form the stockkeeping unit, which routing will be used for the production order.Rallnus (Yamaha FJ1200 - '89 / 25th anniversary was great!)0 -
Rallnus wrote:I'll give you an example.
We are producing an item 4711 at various subsidarie.
For our customers it is the same item, the place of production doesn't matter for the customer.
The routing ist different because we've got different work groups.
If I follow your proposal I should install different items - or not?
Wouldn't I be the right way to build a relationship between stockkeeping units and routings?
(maybe BOM too...)
When we start a production order I will be depending form the stockkeeping unit, which routing will be used for the production order.
Unfortunately Navision Manufacturing does not support Variants, so you need to consider how much work it takes to add variants to manufacturing, and its a HUGE job. For that reason alone you probably need to go to individual items.David Singleton0 -
Rallnus wrote:Wouldn't I be the right way to build a relationship between stockkeeping units and routings?
You're not the only one who would like more flexibility in this area though, there are many companies who would want something like that, or even be able to set up multiple BOMs/Routings based on criteria that have nothing to do with Variants. You're probably aware that BOM/Routing selection has an impact throughout the entire manufacturing system, so making that change is a HUGE task.
You'll probably need to develop this yourself, or perhaps there is a 3rd party product that has this flexibility.0
Categories
- All Categories
- 73 General
- 73 Announcements
- 66.6K Microsoft Dynamics NAV
- 18.7K NAV Three Tier
- 38.4K NAV/Navision Classic Client
- 3.6K Navision Attain
- 2.4K Navision Financials
- 116 Navision DOS
- 851 Navision e-Commerce
- 1K NAV Tips & Tricks
- 772 NAV Dutch speaking only
- 617 NAV Courses, Exams & Certification
- 2K Microsoft Dynamics-Other
- 1.5K Dynamics AX
- 320 Dynamics CRM
- 111 Dynamics GP
- 10 Dynamics SL
- 1.5K Other
- 990 SQL General
- 383 SQL Performance
- 34 SQL Tips & Tricks
- 35 Design Patterns (General & Best Practices)
- 1 Architectural Patterns
- 10 Design Patterns
- 5 Implementation Patterns
- 53 3rd Party Products, Services & Events
- 1.6K General
- 1.1K General Chat
- 1.6K Website
- 83 Testing
- 1.2K Download section
- 23 How Tos section
- 252 Feedback
- 12 NAV TechDays 2013 Sessions
- 13 NAV TechDays 2012 Sessions