about adjust cost for BOM journals
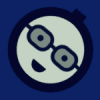
shineyang
Member Posts: 4
Dear all ,
happy new year!
i have a problem need your hepl about adjust cost. i run ad just cost - item entries.it update the item value,but i had run Bom journals to assemble some items to a product. adjust cost can not update the item value for the product assembled from these item?so the product unit cost is error,it must be updated after these items value been adjusted.who can help me? any help is apprciated!
happy new year!
i have a problem need your hepl about adjust cost. i run ad just cost - item entries.it update the item value,but i had run Bom journals to assemble some items to a product. adjust cost can not update the item value for the product assembled from these item?so the product unit cost is error,it must be updated after these items value been adjusted.who can help me? any help is apprciated!
I am shine, Shine and fervency
0
Comments
-
This is not a bug, it's a (known) "feature".
You should use Production BOM in Manufacturing to achieve what you want (by standard app.)
Unless you want to change the code to update the output entries with the (changed) costs of consumed entries.®obi
¯¯¯¯¯¯¯¯¯¯¯¯¯¯¯¯¯0 -
Dear All,
Thank RobertMo's advise.i got solution from MBS,if run BOM journal after perform adjust cost - item entries Batch,the parent item value will updated by component item adjusted value .so,we have to run ajust cost job to adjust component item value, after do this,we can creat BOM journals the parent items value will be correct.i hope this can be useful to one in my the same status . 8) [/b]I am shine, Shine and fervency0 -
But I assume, that you must have all component fully invoiced before running BOM journal... if some purchase invoice is posted after that, product will be not adjusted...0
-
And if you use average costing and you do a positive adjustment to a component after the BOM is processed it may recalculate a new daily average cost and adjust every issue of the component.
What MBS told you is not a solution. The best approach is to use manufacturing BOM's as suggested earlier. Inventory BOM's will possibly only work if you use standard costing, but even that's not foolproof.0 -
Well there could be an option with BOM Journals - Someone takes care about costs manually!
As mentioned before, Standard cost method does help in a way that the cost is not changing all the time, so most of your transactions could be ok. You should be careful only when changing costs.
On the other hand you can try to post every direct/indirect cost of components and running Adjust cost Item Entries job before posting a BOM Journal.
In real life this is hard to achieve. Maybe have more components on stock, so the average age of stock is bigger – this means that when using FIFO you will consume old(er) stock that has probably all costs already posted. Again it is not a guarantee.
Beside that the user who takes care about cost could manually revaluate Outputs, based on some report that shows the cost of components. Again it is very open to errors especially if it is a complex BOM. It can be a hard “excel” job to manually calculate the cost of components (that were really consumed).
As you can se there is a lot of manual work to do and with high possibility of errors. You should consider if it is really not worth to use Manufacturing.®obi
¯¯¯¯¯¯¯¯¯¯¯¯¯¯¯¯¯0
Categories
- All Categories
- 73 General
- 73 Announcements
- 66.6K Microsoft Dynamics NAV
- 18.7K NAV Three Tier
- 38.4K NAV/Navision Classic Client
- 3.6K Navision Attain
- 2.4K Navision Financials
- 116 Navision DOS
- 851 Navision e-Commerce
- 1K NAV Tips & Tricks
- 772 NAV Dutch speaking only
- 617 NAV Courses, Exams & Certification
- 2K Microsoft Dynamics-Other
- 1.5K Dynamics AX
- 320 Dynamics CRM
- 111 Dynamics GP
- 10 Dynamics SL
- 1.5K Other
- 990 SQL General
- 383 SQL Performance
- 34 SQL Tips & Tricks
- 35 Design Patterns (General & Best Practices)
- 1 Architectural Patterns
- 10 Design Patterns
- 5 Implementation Patterns
- 53 3rd Party Products, Services & Events
- 1.6K General
- 1.1K General Chat
- 1.6K Website
- 83 Testing
- 1.2K Download section
- 23 How Tos section
- 252 Feedback
- 12 NAV TechDays 2013 Sessions
- 13 NAV TechDays 2012 Sessions