Adding Manufacturing Costs to Item Costs
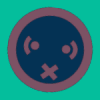
RobbieX
Member Posts: 66
I am hoping to get some advice about adding manufacturing costs to the cost of items at the end of each month.
The company uses Navision 3.6 with SQL server.
The company manufactures items with up to 3 BOM levels. At the end of each month they want to be able to equally distribute the manufacturing costs to all items that were output during the month.
They also want to make sure that when costs are added like this, all sales and consumption are taken into consideration and adjusted accordingly.
For example:
If an item is used to make produce another item then both need to have the cost allocated.
If items from the same output lot are sold in the month then the item cost should be increased.
When items are consumed then the correct reduction in inventory cost should be made.
All the correct entries to make cost adjustments should be made in the value entry table, the G/L entry table, the G/L register, etc.
Can anyone provide some advice about this?
We have tried to use the revaluation journals, calculate inventory value per item ledger entry for the month, allocating costs equally, posting and then running ACIE but the results do not seem to be correct.
Any advice would be greatly appreciated. Thanks.
The company uses Navision 3.6 with SQL server.
The company manufactures items with up to 3 BOM levels. At the end of each month they want to be able to equally distribute the manufacturing costs to all items that were output during the month.
They also want to make sure that when costs are added like this, all sales and consumption are taken into consideration and adjusted accordingly.
For example:
If an item is used to make produce another item then both need to have the cost allocated.
If items from the same output lot are sold in the month then the item cost should be increased.
When items are consumed then the correct reduction in inventory cost should be made.
All the correct entries to make cost adjustments should be made in the value entry table, the G/L entry table, the G/L register, etc.
Can anyone provide some advice about this?
We have tried to use the revaluation journals, calculate inventory value per item ledger entry for the month, allocating costs equally, posting and then running ACIE but the results do not seem to be correct.
Any advice would be greatly appreciated. Thanks.
Robbiex
0
Comments
-
I'll start by saying that what you are describing is possible to do. We have done this for one of our customer and the modification has been in production since the first of the year.
We are taking manufacturing related labor and overhead and pushing it into the inventory value. For example, we pull the labor amount from the time clock system each day and distribute it that day's production on a cost per unit basis.
Your first step need to be a conversion with the accountants. They need to sign-off on a modification like this that impacts the fundemental accounting. What you are talking about here is taking an operating expense and treating it as an asset. Accounting rules can vary between countries so I'm not going to make any assumptions about your situation. All I am saying is clear it with you accountants first.
In our situation, the client is dealing with fresh product that is recieved, processed, and sold within a few days. Very little product is carried across accounting periods. The accoutants told us that for this reason they were OK with this modification. They told us that if the client was producing for inventory that remained on hand for a longer period then this modification would not be acceptable.There are no bugs - only undocumented features.0 -
This will result in a sizable increase in your tranaction volume. Be sure your system is capable of handling that increase and there is adequate processing time avaialble.There are no bugs - only undocumented features.0
-
[Topic moved from Navision forum to Navision Attain forum]Regards,Alain Krikilion
No PM,please use the forum. || May the <SOLVED>-attribute be in your title!0 -
Thanks BB for letting me know that it is possible!
There is no problem from an accounting point of view.
Indeed this sort of modification is often requested in China to suit GAAP.
Can you recommend the best approach?
I would sincerely appreciate any advice you can give me.
Many thanks!Robbiex0 -
Do lots of planning and plan to do lots of testing. Be absolutely surte thing are working as planned before going live. These will not be transactions that can be easily reversed. With our client this modification results in an additional 500,000 value entries each month.
Apply the additional cost only to the inbound (positive) entries. The normal adjust cost process will take care of the outbound entry cost.
The approach we took was to leverage Item Charges. This gave us control over the GL accounts used for posting, plus made it easy to identify the value entries created.There are no bugs - only undocumented features.0
Categories
- All Categories
- 73 General
- 73 Announcements
- 66.6K Microsoft Dynamics NAV
- 18.7K NAV Three Tier
- 38.4K NAV/Navision Classic Client
- 3.6K Navision Attain
- 2.4K Navision Financials
- 116 Navision DOS
- 851 Navision e-Commerce
- 1K NAV Tips & Tricks
- 772 NAV Dutch speaking only
- 617 NAV Courses, Exams & Certification
- 2K Microsoft Dynamics-Other
- 1.5K Dynamics AX
- 320 Dynamics CRM
- 111 Dynamics GP
- 10 Dynamics SL
- 1.5K Other
- 990 SQL General
- 383 SQL Performance
- 34 SQL Tips & Tricks
- 35 Design Patterns (General & Best Practices)
- 1 Architectural Patterns
- 10 Design Patterns
- 5 Implementation Patterns
- 53 3rd Party Products, Services & Events
- 1.6K General
- 1.1K General Chat
- 1.6K Website
- 83 Testing
- 1.2K Download section
- 23 How Tos section
- 252 Feedback
- 12 NAV TechDays 2013 Sessions
- 13 NAV TechDays 2012 Sessions