Floorstock
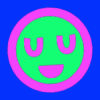
tulsagirl
Member Posts: 2
We are using the floorstock option but are still using PO's to order some of the parts. This is causing a problem with costing since the current cost gets updated when the part is received then gets rolled into the standard cost when we do a roll up and replace. I can see a couple of options. 1--create PO's without part numbers but that means that the data from the part number won't automatically populate. 2--no PO, if we do this then I guess we would just send an email to the vendor and pay the invoice without a PO.
Any suggestions on best practices? Maybe there are other options that I haven't thought of.
Peace
Any suggestions on best practices? Maybe there are other options that I haven't thought of.
Peace
0
Categories
- All Categories
- 73 General
- 73 Announcements
- 66.6K Microsoft Dynamics NAV
- 18.7K NAV Three Tier
- 38.4K NAV/Navision Classic Client
- 3.6K Navision Attain
- 2.4K Navision Financials
- 116 Navision DOS
- 851 Navision e-Commerce
- 1K NAV Tips & Tricks
- 772 NAV Dutch speaking only
- 617 NAV Courses, Exams & Certification
- 2K Microsoft Dynamics-Other
- 1.5K Dynamics AX
- 320 Dynamics CRM
- 111 Dynamics GP
- 10 Dynamics SL
- 1.5K Other
- 990 SQL General
- 383 SQL Performance
- 34 SQL Tips & Tricks
- 35 Design Patterns (General & Best Practices)
- 1 Architectural Patterns
- 10 Design Patterns
- 5 Implementation Patterns
- 53 3rd Party Products, Services & Events
- 1.6K General
- 1.1K General Chat
- 1.6K Website
- 83 Testing
- 1.2K Download section
- 23 How Tos section
- 252 Feedback
- 12 NAV TechDays 2013 Sessions
- 13 NAV TechDays 2012 Sessions