Item Tracking by Location
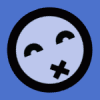
Joe_Mathis
Member Posts: 173
I have been able to make this work by adding a boolean field to the Location card and adding the following code into Codeunit 22.
In the
SetupSplitJnlLine(VAR ItemJnlLine2 : Record "Item Journal Line";VAR PostItemJnlLine : Boolean)
Function.
Before:
Will doing this mess with the Value Entries or Item Ledger Entries?
In my brief testing it appears ok, but I am pretty sure that someone has to have done this before and hopefully can save me a lot of grief later on.
Thank-you very much.
In the
SetupSplitJnlLine(VAR ItemJnlLine2 : Record "Item Journal Line";VAR PostItemJnlLine : Boolean)
Function.
Before:
DisableItemTracking := NOT ItemJnlLine2.ItemPosting; ItemTrackingCode.Code := Item."Item Tracking Code"; ItemTrackingMgt.GetItemTrackingSettings( ItemTrackingCode,ItemJnlLine."Entry Type",ItemJnlLine.Signed(ItemJnlLine."Quantity (Base)") > 0, SNRequired,LotRequired,SNInfoRequired,LotInfoRequired); .........After:
DisableItemTracking := NOT ItemJnlLine2.ItemPosting; ItemTrackingCode.Code := Item."Item Tracking Code"; // Item tracking per location IF Location.GET(ItemJnlLine2."Location Code") THEN BEGIN DisableItemTracking := NOT Location."Use Item Tracking"; IF NOT Location."Use Item Tracking" THEN ItemTrackingCode.Code := ''; END; ItemTrackingMgt.GetItemTrackingSettings( ItemTrackingCode,ItemJnlLine."Entry Type",ItemJnlLine.Signed(ItemJnlLine."Quantity (Base)") > 0, SNRequired,LotRequired,SNInfoRequired,LotInfoRequired); .........
Will doing this mess with the Value Entries or Item Ledger Entries?
In my brief testing it appears ok, but I am pretty sure that someone has to have done this before and hopefully can save me a lot of grief later on.
Thank-you very much.
0
Comments
-
Could you enlighten us as to the business process reasoning behind the modification? Item tracing is used for tracability.
Consider the following scenario:
In this scenario Location A uses Lot Tracking, Location B does not.
1. You purchase 100 cases of Widgets from a supplier. They are received into location A as Lot No. 100.
2. You purchase 100 cases of Widgets from a supplier. They are received into location A as Lot No. 101.
3. You transfer all 200 cases to location B. Location B does not assign Lot numbers.
4. You transfer 100 cases back to Location A. Which lot are they? Are they both lots or a new one?
5. Your supplier issues a recall on the cases received as Lot 100. Where is lot 100?There are no bugs - only undocumented features.0 -
Hi bbrown,
They desire to use it as a packaging system, not an actual quality control system.
A lot equals a pallet of goods.
Currently they do not transfer between locations, so the transfering isn't as important, although it would (actually should) still have the lot tag affixed to it if they wanted to bring it back or to another location that has tracking. If they decide it is something that they desire later on, they can always enable it for that location.
When they produce a lot of goods, they leave it as a lot and sell it as a lot. So they want to be able to pick a lot number and know how much inventory of the item is in that lot and list it on a shipping report/packing list by lots.
Some of their locations are very small, so they don't want to use lots. They would rather maintain the same information manually, I don't fully agree with them, but it is ultimately their decision.
I was looking for problems with the value entries or the item ledger entries, but it looks as though the item tracking is kept on the Item ledger Entry which differentiates by location already, so there shouldn't be an issue. I am doing a lot of entries with this to make sure but was hoping someone had tried something similar and had some advice...0 -
If they never move inventory between locations you will probably be OK. To be safe I would restrict transfers as part of this modification and also make the customer aware of the limitation. I've see many problems resulting from a customer saying "we never do that"There are no bugs - only undocumented features.0
-
Yeah, I have seen a lot of problems start with "No we never do that" in the planning stages and specification and then to "No we never do that unless..." in the actual implementation. No one is happy. It really boils down to "We never do that unless we can make some money."
I have run a series of tests so far without issue.
Sales Orders from multiple locations
Purchase Orders received to multiple locations
Credit Memos
Purchase Credit Memos
Item Journal Entries (Phys Inv etc)
and I am starting on testing Transfer Orders.
If I run into anything, I will probably resrict transfers to be only between locations that are the same in regards to item tracking.
Thanks for your advice.0 -
Hi Joe,
I see this is already an old request, which means you have been running with this for some time now.
Could you share your experience with it ?
I need the same functionality and I was wondering if it is a good idea to do it or not.
thanks for your advice.0 -
We never heard of any problems with this setup. I did take bbrown's advice and limit the transfers between locations...
They were using Item tracking in a non-standard way though, so you would still have to do your own testing and analysis to ensure that it will work in the manner that you expect it to.
This WILL [-X break the item tracing feature as bbrown has stated.0 -
Be aware that if you're using Manufacturing the next line will cause trouble:DisableItemTracking := NOT Location."Use Item Tracking";
Imho this should be:DisableItemTracking := DisableItemTracking OR NOT Location."Use Item Tracking";
Jan Veenendaal0 -
Did anyone who try this hit some wall or it is okay?0
-
BTW our business case is closer to normal tracking, but one simply has to decide what is easier in a given location: to handle all the cases in NAV, or go look up the lot numbers sticked on pallets and cartons in the special cases of transfering back or recalls? All warehouses are outsourced, and in the case of the big central one telling them to go and stick this generated lot number on the pallets and cartons, or telling them to ship 10 pallets of lot number X is okay. For the smaller ones they telling us every time when they ship a small quantity the lot number and then we putting it into NAV is not okay. They should rather just go look it up on the pallets and cartons in the special cases.0
Categories
- All Categories
- 73 General
- 73 Announcements
- 66.6K Microsoft Dynamics NAV
- 18.7K NAV Three Tier
- 38.4K NAV/Navision Classic Client
- 3.6K Navision Attain
- 2.4K Navision Financials
- 116 Navision DOS
- 851 Navision e-Commerce
- 1K NAV Tips & Tricks
- 772 NAV Dutch speaking only
- 617 NAV Courses, Exams & Certification
- 2K Microsoft Dynamics-Other
- 1.5K Dynamics AX
- 320 Dynamics CRM
- 111 Dynamics GP
- 10 Dynamics SL
- 1.5K Other
- 990 SQL General
- 383 SQL Performance
- 34 SQL Tips & Tricks
- 35 Design Patterns (General & Best Practices)
- 1 Architectural Patterns
- 10 Design Patterns
- 5 Implementation Patterns
- 53 3rd Party Products, Services & Events
- 1.6K General
- 1.1K General Chat
- 1.6K Website
- 83 Testing
- 1.2K Download section
- 23 How Tos section
- 252 Feedback
- 12 NAV TechDays 2013 Sessions
- 13 NAV TechDays 2012 Sessions