Manufacturing Overhead?
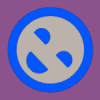
rstols
Member Posts: 28
Can you please help me understand the following about Manufacturing Overhead:
1. How do you set it up so that it become part of the standard cost of an item?
2. How do you process a production order transaction in order to 'book' actual Manufacturing Overhead cost against it?
3. Can you please give me a few exaples of Manufacturing Overheads versus Capacity overheads?
Thank you
1. How do you set it up so that it become part of the standard cost of an item?
2. How do you process a production order transaction in order to 'book' actual Manufacturing Overhead cost against it?
3. Can you please give me a few exaples of Manufacturing Overheads versus Capacity overheads?
Thank you
0
Comments
-
Not totally sure I understand the question, but I'll give it a shot to try help out a fellow Canuck.
Normally overhead is applied to production items as a factor of labour costs.
Labour costs get set up in work centres. Each work centre has a direct unit cost (ie. the labour rate) and an overhead rate ( or %). Let's say your labour rate is $10, and overhead is 50% of labour, then you would put an overhead rate of $5 (or 50%) on the work centre.
When you post an hour of capacity (ie. labour) the system will add $15 to your WIP account. The credit will go wherever you have it setup to go.
You post your labour by using either a capacity journal or a production journal, and posting same.
Not really clear on your question about capacity overheads vs. manufacturing overheads. Capacity is Navision lingo for labour. Normally manufacturing overhead is applied based on labour dollars, therefore they are really two ways of saying the same thing.
Hope this helps. If I've misunderstood your question, please clarify, and I'll try to respond again.0 -
Thank you for the reply from "next door". It helps me but I will explain why I am still confused:
The Production order statistics (F9) shows various cost types of the production order. Navision differentiates between Capacity OH and Manufacturing OH. I couldn't manage to process any transaction where it populates a number in the Manufacturing OH section and therefore don't understand the logic of this.
I appreciate any ideas/suggestions about this.0 -
Did you try putting amounts in the item card under either overhead rate or indirect cost%?
Manufacturing overhead is supposed to represent overhead related to materials costs while capacity overhead is related to capacity (ie. labour costs).0 -
Ok - You're spot on.
Thanks for helping out.0 -
jeffb_r4 wrote:Did you try putting amounts in the item card under either overhead rate or indirect cost%?
Manufacturing overhead is supposed to represent overhead related to materials costs while capacity overhead is related to capacity (ie. labour costs).
Sorry for that, which item field do you mean the overhead rate/indirect cost, the item of product line or raw material item in the component lines?0
Categories
- All Categories
- 73 General
- 73 Announcements
- 66.6K Microsoft Dynamics NAV
- 18.7K NAV Three Tier
- 38.4K NAV/Navision Classic Client
- 3.6K Navision Attain
- 2.4K Navision Financials
- 116 Navision DOS
- 851 Navision e-Commerce
- 1K NAV Tips & Tricks
- 772 NAV Dutch speaking only
- 617 NAV Courses, Exams & Certification
- 2K Microsoft Dynamics-Other
- 1.5K Dynamics AX
- 320 Dynamics CRM
- 111 Dynamics GP
- 10 Dynamics SL
- 1.5K Other
- 990 SQL General
- 383 SQL Performance
- 34 SQL Tips & Tricks
- 35 Design Patterns (General & Best Practices)
- 1 Architectural Patterns
- 10 Design Patterns
- 5 Implementation Patterns
- 53 3rd Party Products, Services & Events
- 1.6K General
- 1.1K General Chat
- 1.6K Website
- 83 Testing
- 1.2K Download section
- 23 How Tos section
- 252 Feedback
- 12 NAV TechDays 2013 Sessions
- 13 NAV TechDays 2012 Sessions