Difference between Production BOM & Item BOM
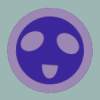
bteredesai
Member Posts: 129
Hi,
Can anyone explain the difference between the Production BOM & Item BOM?
Regards,
Bhushan Teredesai
Can anyone explain the difference between the Production BOM & Item BOM?
Regards,
Bhushan Teredesai
0
Comments
-
Hi,
here is my opinion and answers from help of navision :
A bill of materials can consist of a very large number of components, which can be resources or items. Items can themselves be bills of materials.
Production bills of material can consist of several levels, and you can use a maximum of 50 BOM levels. One production BOM corresponds to one level. The use of other item production BOMs defines the lower levels. The production BOMs are assigned to the item in the Production BOM No. field on the Manufacturing tab of the item card.
Basically, sales and distribution only need item BOM meanwhile manufacturing needs production BOM. you use consumption journal to post material in the production BOM and consumed in the shop floor and use BOM journal and item journal for item BOM.
rgds,
Johnson Alonso
"fight fire with fire"subscribe to:
sea-navision-community-subscribe@yahoogroups.com
detail in:
http://sea-navision-community.blogspot.com0 -
If you use item BOM, you can't have WIP (work in progress Account). Basically when you post the BOM Journal components are used instatenously and finished good is created. You can't have components that are serialized. Since on BOM journal, there is no place to put the serial no, or lot number.
Production BOM has a lot of features, and has WIP and it's a complete manufacturing solution.0 -
ara3n wrote:Production BOM has a lot of features, and has WIP and it's a complete manufacturing solution
do you mean the WIP of production BOM could be seen in the item ledger entries ? or is there another feature in navision represents WIP of item ?
My other opinion about production BOM is it has a calculation to determine qty of item needed. Engineering change order is also available in production BOM, e.g. if you want to change a certain item in a production BOM without delete old production BOM, you can use version feature.
rgds,
Johnson Alonso
"message in blood"subscribe to:
sea-navision-community-subscribe@yahoogroups.com
detail in:
http://sea-navision-community.blogspot.com0 -
And of course, if you use Item BOM, the costs are not distributed through the assembly process. It is same as if you do negative and positive adjustment. But if you use Production BOM and you use the production order to create the product, you can calculate the cost of the product based on cost of the material etc...0
-
As far as I know there are also weakness in both of BOMs. you can't use phantom production BOM in the item BOM and use resource that available in item BOM in the production BOM.
as about application, either production BOM and item BOM can't fully be applied in the chemical industries, brewery industries, petro industries except make some customisations or create add on
rgds,
Johnson Alonso
"the Lord is my Shepherd"subscribe to:
sea-navision-community-subscribe@yahoogroups.com
detail in:
http://sea-navision-community.blogspot.com0 -
Hi,
Production BoM is used in Manufacturing Module and it is essential for the definition of the Finished Goods Item Card. The Item BoM can be used without Manufacturing.
E.G. of use of Item BoM - In case of a trading Organization who deals in say Home Theatre or Computer. The various components may be assembled and sold. In case the organization has to place a purchase order against a demand, you can select the Finished Good Item in the Purchase Order and say Explode BoM. This will give you the break up of the components. You can then place the order for the individual components.
Hope this helps you understand the concept better.
SV0
Categories
- All Categories
- 73 General
- 73 Announcements
- 66.6K Microsoft Dynamics NAV
- 18.7K NAV Three Tier
- 38.4K NAV/Navision Classic Client
- 3.6K Navision Attain
- 2.4K Navision Financials
- 116 Navision DOS
- 851 Navision e-Commerce
- 1K NAV Tips & Tricks
- 772 NAV Dutch speaking only
- 617 NAV Courses, Exams & Certification
- 2K Microsoft Dynamics-Other
- 1.5K Dynamics AX
- 320 Dynamics CRM
- 111 Dynamics GP
- 10 Dynamics SL
- 1.5K Other
- 990 SQL General
- 383 SQL Performance
- 34 SQL Tips & Tricks
- 35 Design Patterns (General & Best Practices)
- 1 Architectural Patterns
- 10 Design Patterns
- 5 Implementation Patterns
- 53 3rd Party Products, Services & Events
- 1.6K General
- 1.1K General Chat
- 1.6K Website
- 83 Testing
- 1.2K Download section
- 23 How Tos section
- 252 Feedback
- 12 NAV TechDays 2013 Sessions
- 13 NAV TechDays 2012 Sessions